- Home
- Business Optimization
- Solutions
- Engineering Solutions
- Fastening on Steel
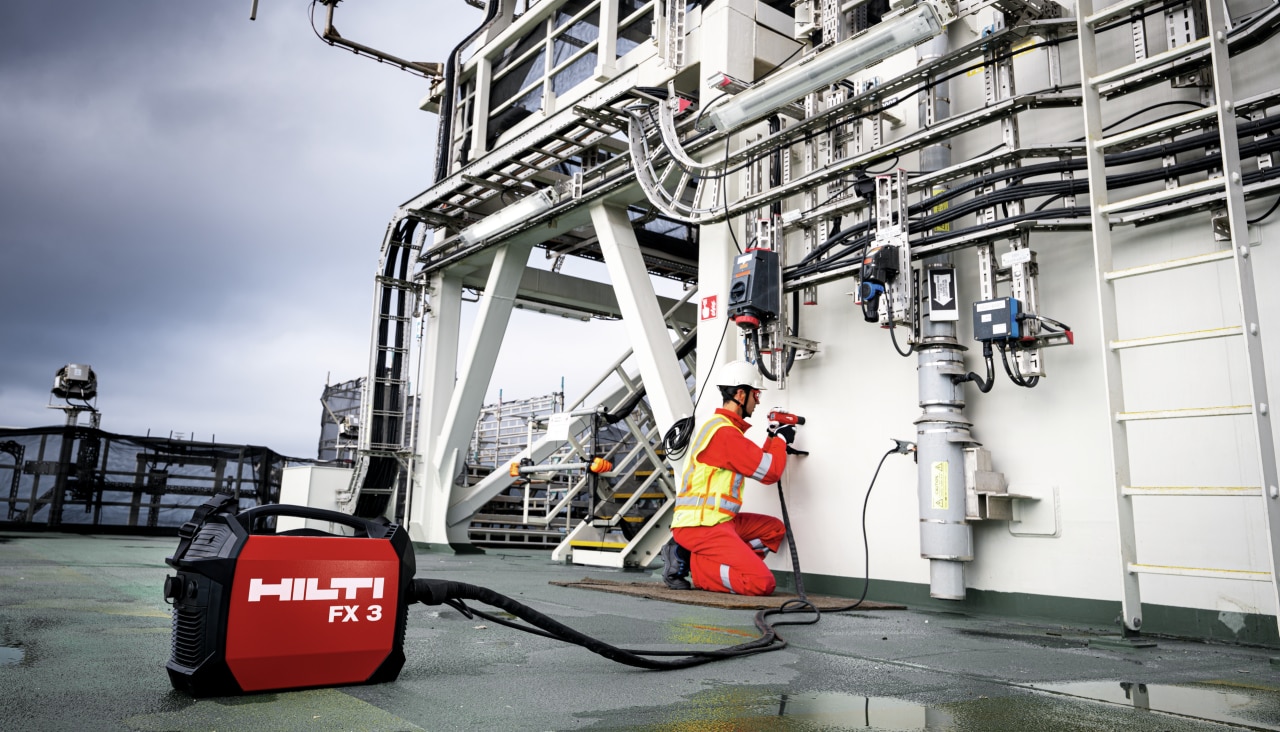
Fastening on steel
Swap traditional welding for speedier, more consistent fastening
Work faster and lower your costs with our solutions for fastening to structural steel. By enabling you to make quick, repetitive fastenings, our systems offer significant advantages over traditional methods such as welding, clamping or through-bolting. And with Hilti cordless Stud Fusion welding you can get the robust, high-quality fastening you need for even tougher applications.
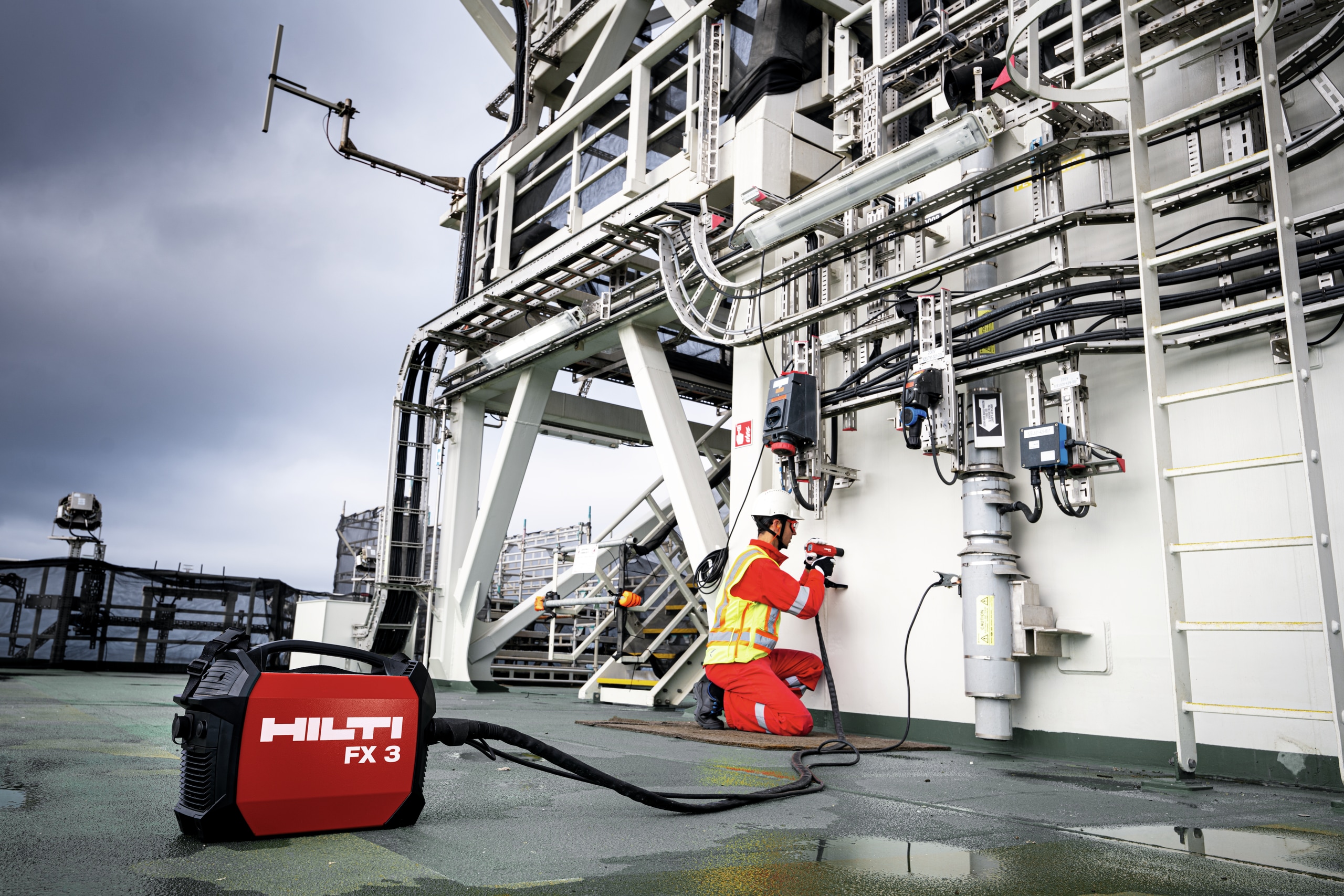
Why choose Hilti for fastening on steel?
Faster and simpler installation
Depending on the technology, installation takes just 1, 2 or 3 steps. Access to only one side of the steel is required and there is either no, or minimal, base material rework. Install faster without compromising corrosion protection.
Higher quality fastenings
Eliminate the trial-and-error of traditional welding thanks to visual aids for surface preparation, guided power regulation on tools, depth gauges for optimum fastener performance and easier inspection using visual check gauges.
Certified welder not required
Fastening to steel with our systems can be completed by trained operators and does not require a certified welder. Welders can be deployed to other critical applications where welding is an absolute must.
Safer tool operation
Help protect your crews: the elimination of angle grinders, sparks and power cables helps reduce the risk of cuts and burns as well as fire and tripping hazards.
Extra product reliability
We provide comprehensive technical data for each product. This data is backed by various independent code authorities and globally recognized type approval bodies.
More flexibility in the field
Our solutions can be used in most weather conditions. And because the tools use powder or battery technology you don't need an external power source. That means more portability on the jobsite.
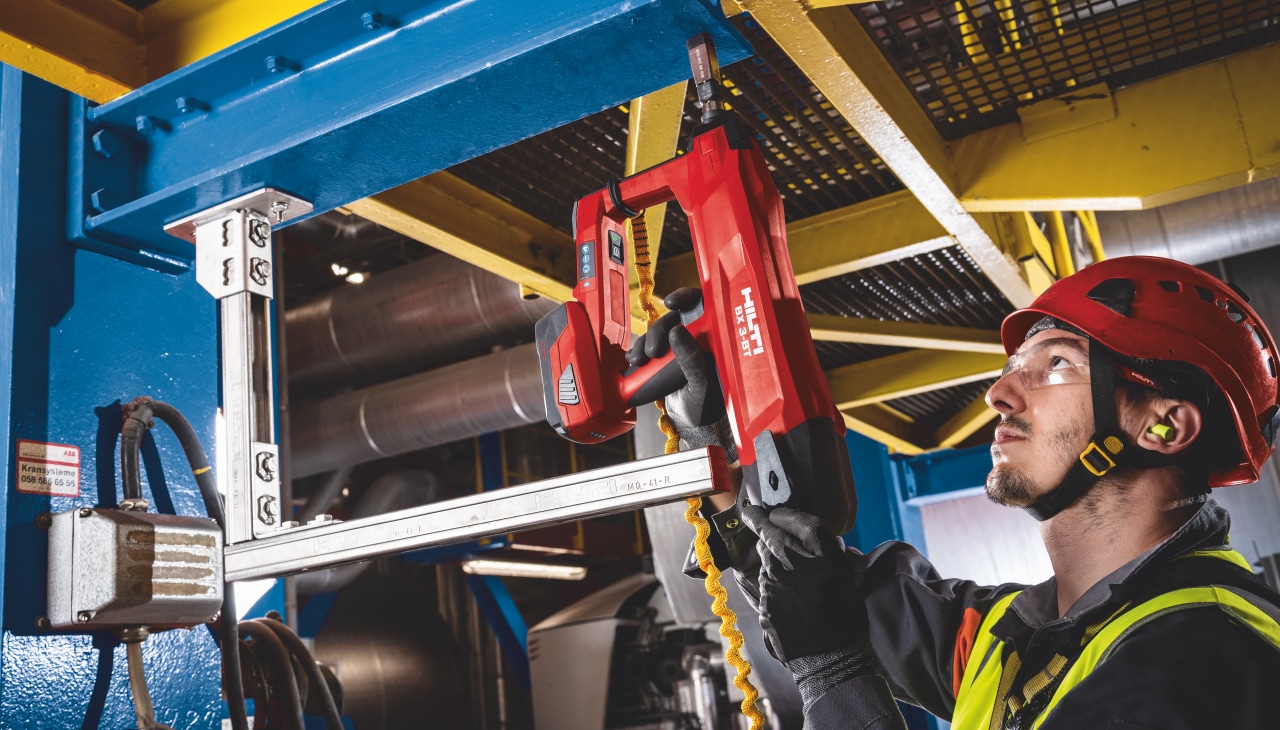
Fastening on steel applications
Solutions for offshore and onshore oil and gas, shipbuilding and more
Our solutions are designed for key applications across many industries and corrosive environments. They include:
- Installing grating and diamond plate
- Fastening of non-critical pipe and cable tray/ladder support structures
- Fastening of electrical connections for grounding and bonding
- Shipbuilding applications including standoff support, false ceilings, and fastening of equipment, furniture and outfitting
Which solution is right for your application?
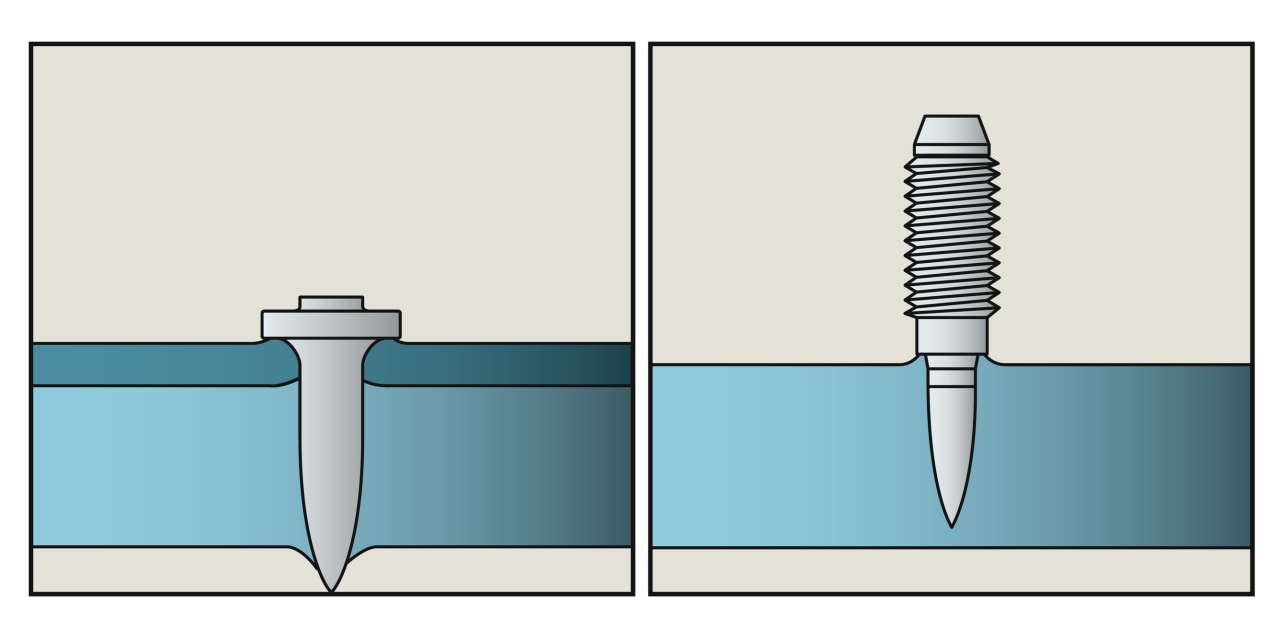
Sharp tip fastening
A cost-competitive, one-step solution for high-frequency fastening where speed is critical.
How it works:
With X-R or X-ST sharp tip fastening, a sharp tip stainless steel fastener is driven by a powder-actuated tool into the base material, creating a high-quality connection.
Benefits:
- Stainless steel fasteners for mildly corrosive environments where penetration through base material is acceptable
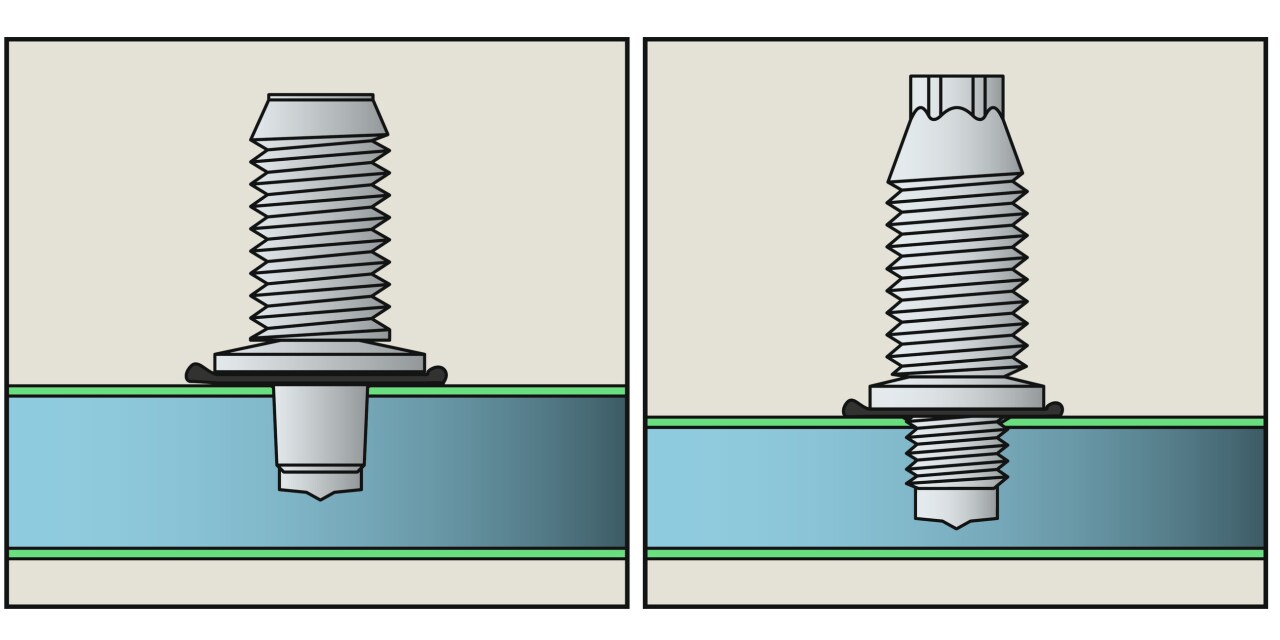
Blunt tip fastening
Versatile 2-step solutions for daily fastening to steel across a broad range of applications.
How it works:
With X-BT or S-BT blunt tip fastening, a threaded fastener is driven or screwed into a pre-drilled hole in the base material by a powder or battery-powered tool.
Benefits:
- No damage to corrosion protection in non-through penetration applications
- Fastening in under 2 minutes
- Stainless steel fasteners – equivalent corrosion protection as A4 (316) for highly-corrosive environments
- Duplex coated carbon steel fastener for mildly-corrosive environments
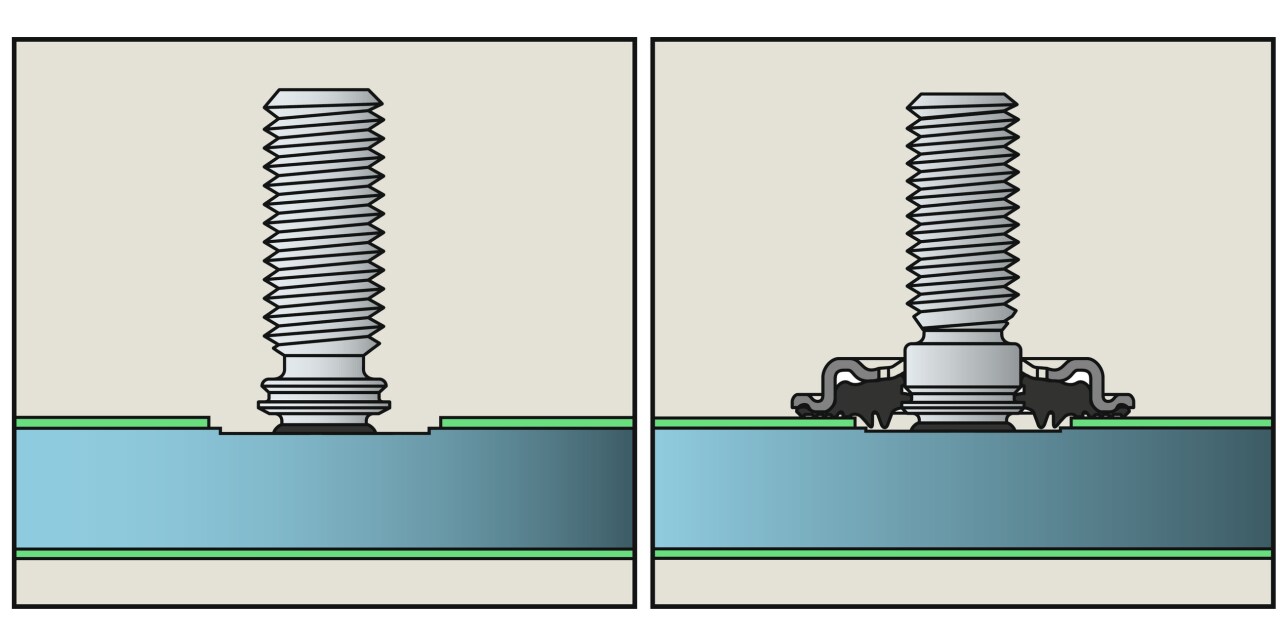
Fusion welding
For high-end fastening to steel in demanding, engineered applications – combines welding performance with ease of use.
How it works:
With F-BT fusion welding, a threaded stud is welded by a battery-powered tool on a prepared surface. The optional washer then seals the prepared surface for a fastening point with long-term corrosion resistance.
Benefits:
- No damage to rear side of corrosion protection coating and simple front side sealing so no rework is required
- No drilling or notching required, helping maintain base material integrity
- High-load, thin base and versatile fastening point
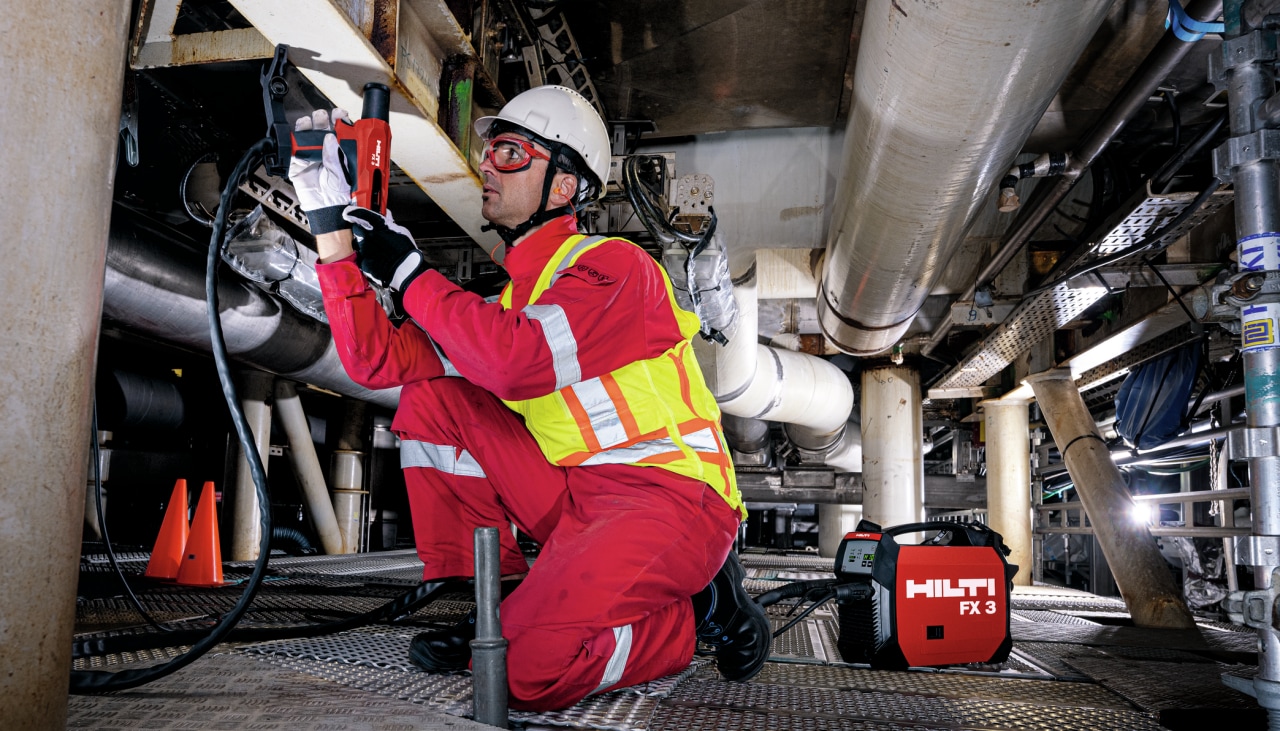
Welding performance minus the pain
Speed up tougher fastening jobs and boost design efficiency with Hilti Stud Fusion
For applications with higher tensile loads or thinner base materials, choose Hilti Stud Fusion. You won't need certified welders and you can avoid the high costs and rework associated with traditional welding. The cordless system is fully mobile and real-time feedback on the tool makes it easier to get more reliable and consistent fastenings.
To simplify your fastener specification, access our extensive library of calculations for pre-designed 'typical' support structure configurations. You can also use our powerful software tools to optimize your fastener design, or get full engineering support from our expert design teams.